The Washington Dept. of Transportation’s Shoreline Traffic Management Center (TMC) is one of six regional operation centers of the Intelligent Transportation Systems (ITS) used to make Washington’s roads more safe and efficient. ITS devices include roadside cameras, ramp meters, variable message signs, speed and lane control signs, and radios.
When the TMC outgrew its building – as well as the size of its roadway monitoring system – the staff realized it was time not just for a physical upgrade, but a technological one, too.
The Tech Decision
WSDOT tested multiple displays, designed the configuration of the displays then wrote an RFQ specifying the equipment and installation services required for their project. WSDOT then engaged CompView’s Seattle office for the installation. CompView worked with WSDOT a few years ago on a smaller video wall project.
The installation took place in 2 phases; phase 1 occurred in 2015 and phase 2 in the spring of 2016. Both CompView and Forbis said the installation overall went very well, with a few last-minute workarounds to accommodate.
As CompView installed the monitors on the walls, the team discovered the sheet metal in the false wall built to hold the brackets didn’t go up as high as they thought. The top row of monitors needed extra support, so CompView worked with the client and general contractor to resolve the issue.
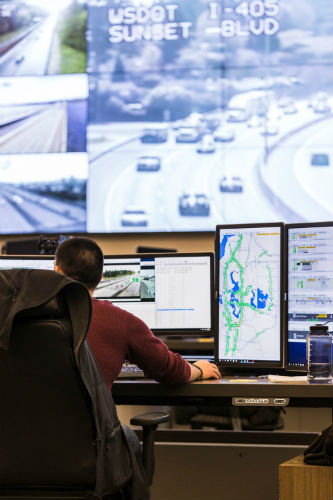
Prior to arriving on-site, CompView provided the 90 OPS docking stations, video processors and computers to WSDOT for programming. WSDOT then returned the programmed OPS computers to CompView for installation.
Phase 1, required meticulous coordination and installation integration of the 90 displays which were aligned and placed at exact heights and spacing intervals. The project manager and team worked closely with Michael Forbis to verify calculations, make adjustments to alignment and cable management then test the displays.
For phase 2, CompView installed the 2×3 videowall while the TMC was fully operational and worked with Michael to ensure the least possible disruption to the team. In the event of a traffic emergency, WSDOT would notify CompView to stop work to eliminate disruption.
CompView partnered with Vistacom for the Barco system which drives the video wall content. The Barco system shipped to Vistacom for configuration and testing then to CompView for installation on-site. CompView then coordinated with Vistacom and the client for training.
Jackie McNeice, installation manager for CompView, says that Forbis and his team exhibited an “exceptional” level of preparedness. “He anticipated what we needed for seamless integration, from power and storage, to identifying space for server rooms,” she says. “Michael and WSDOT were also flexible and understanding problem solvers.”
The Solution
The new TMC contains a 3×4 video wall and 90 individual displays which give employees a way to view current conditions of freeways, tunnels and bridges and collaborate on incident response.
The video comes from the approximately 750 cameras in the WSDOT system and traffic detectors on the highways, giving a real-time picture of traffic conditions. A display console is set up for the traffic signal operations group, which uses traffic data and live video from the cameras to change the timing of traffic signals when there are incidents or unexpected congestion.
There also are several control functions for road signs all over the state, such as signage showing the variable toll rates; as a roadway gets more congested, the express toll lane’s price fluctuates, and employees can instantly update the signage to reflect the price.
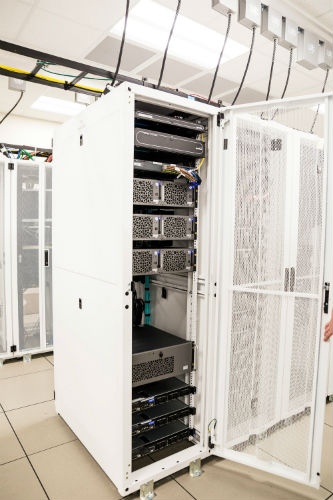
Other monitoring operations include the roadways and pedestrian walkways inside tunnels, which are monitored 24/7. As WSDOT employees see issues like truck load spills or pooling water, its radio operators can dispatch field workers to pick up spills or unclog drains. There is also a console WSDOT shares with area transit officials.
The Impact
Both CompView and Forbis said the installation overall went very well, with a few last-minute workarounds to accommodate.
For example, as CompView was installing the monitors on the walls, the team discovered that the sheet metal in the false wall built to hold the brackets didn’t go up as high as they thought.
“The building has a two-foot raised floor, and when they laid the steel in the false wall to mount the brackets, we thought we had a foot or two to play with, but the sheet metal was actually measured from the concrete floor,” Forbis says. “So the top row of monitors needed some extra support, and we had to deal with that.”
Another quirk was due to the building’s geographical location in the Pacific Northwest.
“The building came with an earthquake requirement, so we had to run the mounting by a structural engineer to make sure the monitors would stay on the walls in case of an earthquake,” Forbis says.
CompView installed the 2×3 videowall while the TMC was fully operational and worked with Michael to ensure the least possible disruption to the team.
Jackie McNeice, installation manager for CompView, said that Forbis and his team exhibited an “exceptional” level of preparedness.
“He anticipated what we needed for seamless integration, from power and storage, to identifying space for server rooms,” she says. “Michael and WSDOT were also flexible and understanding problem solvers which made it a very easy project.”
If you enjoyed this article and want to receive more valuable industry content like this, click here to sign up for our digital newsletters!
Washington’s TMC is making a huge use of technology & Digital display solutions. It was nice to read, thanks for sharing.